Understanding the intricate relationship between architectural design and project expenses is crucial for anyone involved in construction. This discussion explores how seemingly small decisions made during the planning phase can have a significant impact on the overall budget. From material selection to the complexity of the design, every architectural choice contributes to the final cost of a project.
We will examine various facets of this relationship, including the implications of material selection, the financial burden of complex designs, and the influence of energy efficiency on long-term operational costs. Moreover, we will explore how factors like labor costs, site considerations, and technological integration further shape the financial landscape of a building project. This analysis will provide valuable insights for architects, developers, and clients alike, enabling them to make informed decisions that balance design aspirations with budgetary constraints.
Initial Project Planning and Design Phase Impact
The initial project planning and design phase is arguably the most critical stage in determining the overall cost of a construction project. Decisions made early on have a ripple effect, influencing material selection, construction methods, labor requirements, and ultimately, the final budget. Failing to consider cost implications during this phase can lead to significant overruns and project delays.
Early Design Decisions Influence on Project Expenses
Early design decisions set the foundation for the entire project. These decisions encompass a wide range of aspects, including site selection, building footprint, structural systems, and material choices. Each decision carries a cost implication, and poorly considered choices can lead to escalating expenses throughout the project lifecycle. For example, choosing a complex building shape can increase the cost of formwork, labor, and materials compared to a simpler, more regular design.
Similarly, selecting a specific structural system, such as a steel frame versus a concrete frame, will have significant cost implications related to material prices, fabrication, and installation.
Architectural Choices That Escalate Costs During the Initial Planning Stage
Certain architectural choices are known to drive up project costs if not carefully managed during the initial planning stage. These include:
- Complex Geometries: Buildings with irregular shapes, curves, and complex angles necessitate specialized formwork, cutting, and fabrication. This increases material costs, labor hours, and the potential for errors. For instance, a building with a curved facade will require more expensive and specialized glass and framing systems compared to a building with a flat facade.
- Unnecessary Material Specifications: Specifying premium materials, such as imported stone or custom-made finishes, without considering the budget can significantly inflate costs. Often, equivalent or even superior performance can be achieved with more cost-effective, locally sourced alternatives.
- Overly Ambitious Structural Systems: While innovative structural designs can be aesthetically pleasing, they can also be significantly more expensive to implement. This includes designs that require long spans, cantilevers, or unusual support systems. Each of these aspects adds complexity and cost.
- Lack of Standardization: Custom designs and non-standardized components increase costs by requiring specialized manufacturing, longer lead times, and potentially, increased labor costs during construction. Standardized components, such as doors, windows, and fixtures, are generally more cost-effective.
- Inadequate Site Analysis: Insufficient site investigations can lead to unforeseen challenges during construction, such as unstable soil conditions or the need for extensive excavation. These unexpected issues can cause significant cost overruns. For example, if a site analysis fails to identify the presence of underground utilities, their unexpected discovery during excavation can lead to costly delays and modifications.
Methods for Cost-Effective Design During the Initial Planning Stage
Employing specific strategies during the initial planning stage can help to achieve cost-effective designs. These include:
- Value Engineering: Value engineering is a systematic approach to analyze the project’s design and identify opportunities to reduce costs without compromising functionality or quality. This process involves examining each component of the design to determine if there are more cost-effective alternatives.
- Early Collaboration with Contractors: Involving contractors early in the design process allows for valuable input on construction methods, material availability, and potential cost savings. This collaborative approach can help to identify potential problems early on and develop more efficient and cost-effective solutions.
- Standardization and Modular Design: Utilizing standardized components and modular design principles can help to reduce material costs, construction time, and labor requirements. This approach also simplifies the design process and reduces the potential for errors.
- Detailed Cost Estimating: Developing detailed cost estimates throughout the design process allows for the identification of potential cost overruns early on. These estimates should be based on accurate data and should include allowances for contingencies.
- Life-Cycle Cost Analysis: Considering the long-term operating and maintenance costs of different design options can help to make informed decisions that minimize overall costs. For example, selecting energy-efficient building systems can reduce utility bills over the building’s lifespan, offsetting the initial higher cost.
Material Selection and Cost Implications
The selection of building materials significantly influences project budgets, impacting both initial construction costs and long-term operational expenses. Material choices affect not only the immediate price of components but also factors such as labor costs, transportation, maintenance requirements, and the building’s lifespan. Careful consideration of these factors is crucial for effective cost management throughout the project lifecycle.Material selection involves a complex interplay of factors, from aesthetics and structural performance to environmental impact and lifecycle costs.
Understanding the cost implications of various materials is paramount for making informed decisions that align with budgetary constraints and project goals.
Cost Comparison of Building Materials
The cost of building materials varies significantly, influenced by factors such as supply chain dynamics, geographical location, and market fluctuations. Comparing materials based on cost per unit, durability, and environmental impact provides a comprehensive view for informed decision-making.
Material | Cost per Unit (Approximate) | Durability | Environmental Impact |
---|---|---|---|
Concrete | $80 – $150 per cubic yard | High (can last for decades with proper maintenance) | Moderate to High (high embodied carbon due to cement production; can be mitigated with recycled aggregates and supplementary cementitious materials) |
Steel | $0.70 – $1.20 per pound | High (strong and resistant to various environmental factors) | High (significant energy consumption during production; can be reduced with recycled steel) |
Wood (e.g., softwood lumber) | $5 – $20 per board foot (varies greatly depending on species and grade) | Variable (depends on species, treatment, and application; can range from moderate to high) | Moderate to Low (generally considered a renewable resource; can sequester carbon; requires responsible forestry practices) |
Brick | $0.50 – $1.00 per brick | High (durable and resistant to fire) | Moderate (energy-intensive manufacturing process) |
Aluminum | $1.50 – $3.00 per pound | High (corrosion-resistant and lightweight) | High (significant energy consumption during production; can be reduced with recycled aluminum) |
Note: Cost figures are approximate and can vary significantly based on location, market conditions, and specific product specifications. Durability refers to the material’s resistance to wear, tear, and environmental factors over time. Environmental impact considers factors such as embodied carbon, resource depletion, and potential for recyclability.
Sustainable Material Options and Cost Impact
Embracing sustainable materials can contribute to environmental responsibility while influencing project costs in various ways. While some sustainable options may have higher initial costs, they often offer long-term benefits, such as reduced operational expenses and enhanced building value.
- Recycled Concrete Aggregates: Using recycled concrete aggregates in new concrete mixtures can reduce the demand for virgin materials, lowering environmental impact. The initial cost may be slightly lower than using virgin aggregates, depending on local availability and processing costs.
- Cross-Laminated Timber (CLT): CLT, a sustainable wood product, offers excellent structural performance and aesthetic appeal. While the upfront cost can be higher than traditional materials like steel or concrete, the speed of construction and reduced labor costs can partially offset the initial investment. For example, a study comparing CLT to concrete for a multi-story building in Europe found that while CLT had a slightly higher material cost, the overall construction time was reduced by approximately 20%, leading to lower labor expenses.
- Reclaimed Wood: Reclaimed wood, sourced from old buildings or salvaged materials, provides a unique aesthetic and reduces the demand for new timber. While sourcing and processing reclaimed wood can be more labor-intensive, the cost can be competitive, and it contributes to a lower environmental footprint.
- Low-Embodied Carbon Concrete: Using supplementary cementitious materials (SCMs) like fly ash or slag in concrete mixtures reduces the amount of cement needed, lowering the embodied carbon footprint. The cost of these materials is often comparable to or lower than that of Portland cement, resulting in a potentially lower overall cost.
- Bamboo: Bamboo is a rapidly renewable resource with high tensile strength. It can be used for various applications, including structural components and flooring. The cost of bamboo products can be competitive with traditional materials, and the environmental benefits are significant due to its rapid growth rate.
Building Complexity and Its Financial Burden
Architectural complexity significantly escalates construction costs. Intricate designs, while often aesthetically pleasing, introduce challenges that directly translate into higher expenses. These costs stem from increased labor requirements, specialized materials, and the need for advanced construction techniques. The more complex the design, the more potential there is for cost overruns and delays.
Impact of Complex Architectural Designs on Construction Expenses
Complex designs inherently drive up construction expenses due to several factors. These factors include the increased labor hours required for precise execution, the need for specialized contractors with expertise in non-standard construction methods, and the potential for delays caused by unforeseen challenges.
- Increased Labor Costs: Complex designs necessitate more skilled labor and a greater number of man-hours. Precision is paramount, leading to slower construction processes and higher hourly rates for specialized trades.
- Specialized Materials: Intricate forms often require custom-fabricated components and unique materials. These materials are typically more expensive than standard options and may have longer lead times.
- Advanced Construction Techniques: Complex geometries demand sophisticated construction techniques, such as 3D modeling, advanced formwork, and specialized equipment. These techniques add to the overall cost.
- Potential for Delays: The intricate nature of complex designs increases the likelihood of unforeseen challenges during construction, leading to delays and associated costs, such as penalties and extended overhead.
- Change Orders: Complex projects often experience a higher number of change orders, which further contribute to cost escalation. These changes, driven by unforeseen site conditions or design modifications, add time and expense.
Additional Costs Associated with Intricate Building Facades or Unusual Structural Forms
Intricate building facades and unusual structural forms contribute to increased construction costs through several channels, primarily through the specialized materials, complex labor, and advanced engineering required for their implementation. These architectural elements often require careful planning and execution to ensure structural integrity and aesthetic appeal.
- Custom Fabrication: Unusual forms frequently necessitate custom fabrication of structural components, cladding, and other elements. This custom work increases material costs and fabrication time.
- Specialized Labor: The installation of intricate facades and structural forms requires highly skilled labor, including specialized tradespeople like facade installers, steelworkers, and concrete specialists. Their expertise commands higher wages.
- Engineering and Design Fees: The design and engineering of complex structural forms involve more complex calculations, analysis, and detailing. This increases design fees and the need for specialized consultants.
- Testing and Inspection: The construction of unusual forms often requires more rigorous testing and inspection to ensure structural integrity and adherence to building codes. These inspections add to the overall cost.
- Waste and Material Handling: The complexity of the designs often results in increased material waste and requires specialized waste management practices, which add to the cost.
Hypothetical Building Design Comparison: Simple vs. Complex
Consider two hypothetical office buildings, each with a similar square footage and intended functionality, but with vastly different architectural designs. The first building will be designed with a simple, rectangular form and a straightforward facade. The second building will incorporate a curved facade, complex rooflines, and a series of irregular structural elements.
Cost Category | Simple Design (Estimated Cost) | Complex Design (Estimated Cost) |
---|---|---|
Materials | $1,500,000 | $2,500,000 |
Labor | $2,000,000 | $3,500,000 |
Engineering & Design | $250,000 | $500,000 |
Specialized Equipment | $100,000 | $300,000 |
Contingency (10%) | $385,000 | $680,000 |
Total Estimated Cost | $4,235,000 | $7,480,000 |
The table demonstrates a substantial difference in estimated costs between the two designs. The complex design, with its irregular facade, requires more specialized materials, skilled labor, and advanced engineering, leading to a significantly higher overall cost.
In this hypothetical scenario, the complex design’s total cost is almost double that of the simple design. This highlights the significant financial burden associated with architectural complexity.
The construction cost difference between a simple and complex design can easily be 30% to 100% or more, depending on the specific complexities involved.
Energy Efficiency and Long-Term Operational Costs
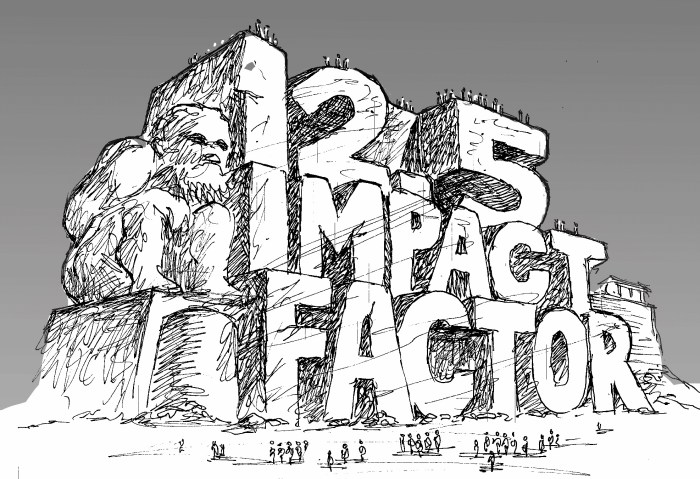
The integration of energy-efficient design is crucial for minimizing both initial construction costs and long-term operational expenses. While energy-efficient features often require a higher upfront investment, the resulting reduction in energy consumption can lead to significant savings over the lifespan of a building. This section explores how these design choices impact costs, examines different energy-saving technologies, and demonstrates the financial benefits of sustainable design.
Upfront Costs vs. Long-Term Savings: An Overview
Energy-efficient designs typically involve higher initial costs due to the implementation of advanced technologies and materials. However, these upfront investments are often offset by substantial long-term savings. Lower energy bills, reduced maintenance expenses, and potential government incentives contribute to the overall financial benefits. The return on investment (ROI) period varies depending on the specific technologies and building characteristics.
Energy-Saving Technologies and Associated Expenses
Various technologies contribute to energy efficiency in buildings, each with its own cost implications. Here’s a comparison of some key technologies:
- High-Performance Insulation: While more expensive than standard insulation, high-performance insulation significantly reduces heat transfer, leading to lower heating and cooling demands. The upfront cost can range from 10% to 20% higher than conventional insulation, but annual energy savings can be substantial, typically ranging from 15% to 30%, depending on climate and building design. For example, a study by the U.S.
Department of Energy showed that upgrading insulation in a typical home could reduce energy bills by several hundred dollars annually.
- Energy-Efficient Windows: These windows utilize features like double or triple-pane glass, low-emissivity coatings, and gas fills (argon or krypton) to minimize heat loss and gain. The initial cost can be 20% to 40% higher than standard windows. However, they can reduce energy consumption for heating and cooling by 10% to 25%, resulting in long-term savings and improved comfort.
- High-Efficiency HVAC Systems: These systems, including heat pumps and high-efficiency furnaces, use advanced technology to deliver heating and cooling more efficiently. While the initial cost is higher (potentially 25% to 50% more than standard systems), they consume significantly less energy. The energy savings can range from 20% to 40%, leading to lower monthly utility bills.
- LED Lighting: LED lighting is more expensive to purchase initially than traditional incandescent or fluorescent bulbs. However, LEDs use up to 75% less energy and last much longer. The upfront cost is often offset by reduced energy consumption and lower replacement costs. The lifespan of an LED bulb can be up to 25,000 hours, compared to 1,000 hours for an incandescent bulb.
- Solar Panels: Solar panels have a significant upfront cost, including the panels, installation, and any necessary grid connections. However, they generate renewable energy, reducing or eliminating reliance on the utility grid. Over time, the savings on electricity bills can be substantial, and government incentives like tax credits and rebates can further reduce the payback period. The payback period can vary from 5 to 10 years, depending on local solar resources and electricity rates.
- Smart Building Controls: Smart building controls, such as automated thermostats and lighting systems, allow for optimized energy usage. While the initial investment in these systems can be moderate, they can lead to significant energy savings by adjusting systems based on occupancy and environmental conditions. Energy savings of 10% to 30% are common.
Financial Benefits of Sustainable Design and Operational Expenses
Incorporating sustainable design principles offers several financial benefits that reduce operational expenses over the building’s lifespan.
- Reduced Utility Bills: Energy-efficient buildings consume less energy for heating, cooling, lighting, and other operations. This directly translates to lower utility bills, providing substantial cost savings over time.
- Lower Maintenance Costs: Sustainable design often incorporates durable materials and systems that require less maintenance. For example, LED lighting has a longer lifespan than traditional bulbs, reducing replacement costs.
- Increased Property Value: Energy-efficient buildings are often more attractive to buyers and tenants, leading to higher property values. Studies have shown that green buildings can command higher rental rates and selling prices.
- Government Incentives and Rebates: Many governments offer financial incentives, such as tax credits and rebates, to encourage the construction and renovation of energy-efficient buildings. These incentives can significantly reduce the upfront costs of implementing sustainable design features.
- Improved Occupant Health and Productivity: Sustainable buildings often feature better indoor air quality and natural lighting, leading to improved occupant health and productivity. This can translate into lower healthcare costs and increased employee productivity.
Labor Costs and Architectural Design Influence
Architectural design significantly impacts construction labor requirements and, consequently, the overall project cost. Design choices can either streamline the construction process, reducing labor hours and expenses, or introduce complexities that increase both. Understanding this relationship is crucial for architects and clients seeking to optimize construction budgets.
Impact of Architectural Design on Labor Requirements
The architectural design directly influences the amount of labor required for a project by dictating the complexity of the building’s structure, the types of materials used, and the level of detail involved in the construction. Designs with intricate geometries, unusual shapes, or complex systems often necessitate specialized skills and extended construction times, driving up labor costs. Conversely, designs that prioritize simplicity and standardization can lead to faster construction, reduced labor needs, and lower expenses.
Design Features That Increase Construction Labor Hours
Certain design features inherently increase construction labor hours.
- Complex Geometries: Buildings with non-standard angles, curves, or irregular shapes require more time and precision for fabrication and assembly. For instance, constructing a curved facade involves specialized formwork and more meticulous placement of materials compared to a flat, rectangular wall.
- Intricate Detailing: Highly detailed designs, such as elaborate cornices, custom millwork, or complex facade patterns, demand significant labor for their execution. Each detail necessitates individual attention and skilled craftsmanship, extending the construction timeline.
- Unconventional Material Choices: Using unfamiliar or difficult-to-work-with materials can increase labor hours. For example, using precast concrete panels with intricate designs often requires more labor than using standard brick or concrete block.
- Repetitive Tasks: While seeming simple, designs that require extensive repetition of a single task, like installing numerous small tiles or repetitive decorative elements, can also significantly increase labor hours due to the cumulative time spent on each instance.
- Poor Coordination of Services: Designs that do not adequately consider the integration of mechanical, electrical, and plumbing (MEP) systems can lead to delays and rework. This can happen if there are clashes between the systems or if access for installation and maintenance is limited, causing additional labor costs to resolve these issues.
Procedures for Optimizing Labor Efficiency and Reducing Expenses
Several procedures can be implemented during the design phase to optimize labor efficiency and minimize construction expenses.
- Prioritize Simplicity and Standardization: Designs that utilize simple geometric forms, repetitive elements, and standard construction techniques can significantly reduce labor requirements. This approach allows for faster construction and minimizes the need for specialized labor.
- Employ Modular Design: Utilizing modular components and prefabricated elements can streamline the construction process. Prefabricated wall panels, roof trusses, and other modules can be manufactured off-site and assembled quickly on-site, reducing labor hours and improving efficiency.
- Choose Materials Wisely: Selecting materials that are easy to work with, readily available, and require minimal on-site processing can help reduce labor costs. Consider materials that are pre-finished, pre-cut, or come in standardized sizes.
- Optimize Building Systems Integration: Designing with MEP systems integration in mind from the outset is crucial. This includes coordinating the placement of ductwork, wiring, and plumbing to minimize clashes and ensure easy access for installation and maintenance. This can involve using Building Information Modeling (BIM) to simulate the construction process.
- Foster Collaboration and Communication: Encouraging close collaboration between architects, engineers, contractors, and subcontractors from the design phase through construction is critical. Effective communication helps to identify and resolve potential issues early on, preventing costly rework and delays.
- Consider the “Buildability” of the Design: Architects should always consider how easily a design can be built. This includes evaluating the availability of skilled labor, the feasibility of construction techniques, and the accessibility of the site.
Site Considerations and Design Adaptations
Architectural design is profoundly influenced by the specific characteristics of the building site. These site conditions directly impact the design process, construction techniques, and ultimately, the overall project cost. Understanding these factors is crucial for making informed decisions that balance aesthetic goals with budgetary constraints.
Influence of Site Conditions on Design and Cost
The physical characteristics of a building site significantly dictate the architectural design and construction methods. These characteristics include the terrain, soil composition, and environmental factors, each influencing design choices and associated costs.
- Terrain: Sloping sites, for example, necessitate retaining walls, extensive grading, and potentially complex foundation systems. These elements add to the construction expenses. Conversely, a flat site offers simpler construction processes, reducing costs related to earthwork and foundation complexities.
- Soil Type: The soil’s load-bearing capacity is a critical factor. Poor soil conditions, such as expansive clay or loose sand, require specialized foundations like pile foundations or soil stabilization techniques. These methods are considerably more expensive than traditional spread footings used on stable soil. Conversely, stable soil allows for simpler, more cost-effective foundation designs.
- Environmental Factors: Sites prone to flooding or seismic activity necessitate designs that incorporate specific protective measures. For example, buildings in flood zones require elevated foundations or flood-resistant construction materials, increasing costs. In seismic zones, structures need reinforced designs to withstand earthquakes, further escalating expenses.
Cost Implications of Building on Challenging Sites
Constructing on a challenging site presents a variety of cost implications compared to building on a more straightforward one. These cost differences often arise from the need for specialized construction techniques, increased material requirements, and extended construction timelines.
- Foundation Costs: Difficult sites typically demand more complex and expensive foundation systems. This might include the use of piles, caissons, or raft foundations to overcome poor soil conditions.
- Earthwork and Grading: Sloping sites necessitate extensive earthmoving to create a level building platform. This involves excavation, backfilling, and grading, which can be a significant cost driver.
- Material Costs: Challenging sites may require specialized materials, such as reinforced concrete or waterproof membranes, to address specific site conditions. These materials often come at a premium.
- Labor Costs: Construction on difficult sites often involves more labor-intensive processes, requiring specialized skills and equipment. This can lead to higher labor costs.
- Permitting and Regulatory Requirements: Building on challenging sites often involves more stringent permitting requirements and inspections, which can add to the overall project cost and timeline.
Design Adaptation for a Difficult Site: Example
Consider designing a residential building on a steeply sloping site with unstable soil. This scenario necessitates several design adaptations that impact expenses.
- Design on Difficult Site: The design would likely incorporate a terraced structure to follow the natural slope, minimizing the need for extensive excavation. The foundation system would likely utilize a combination of retaining walls to stabilize the slope and pier foundations to provide support on the unstable soil. The building would be constructed with lightweight materials to reduce the load on the foundations.
This design requires specialized construction techniques, including soil stabilization methods, advanced drainage systems, and potentially, the use of engineered lumber.
- Design on Easy Site: In contrast, if the same residential building were to be constructed on a flat site with stable soil, the design would be significantly simpler. A traditional foundation system (spread footings) could be used, and the building footprint could be rectangular. The construction process would be more straightforward, reducing the need for specialized equipment and labor. This design could utilize standard construction materials, and the overall construction time would be shorter.
- Cost Comparison: The difficult site design would likely incur substantially higher costs due to the specialized foundation, extensive earthwork, and need for specialized materials. Estimates for a similar-sized house on the challenging site could be 20-40% higher than the cost on the easier site, depending on the degree of the site’s challenges.
Technological Integration and Cost Factors
The integration of technology in modern architecture has become increasingly prevalent, promising enhanced functionality, efficiency, and user experience. However, these advancements come with associated costs that must be carefully considered throughout the design and construction phases. Understanding the financial implications of incorporating smart technologies is crucial for making informed decisions and optimizing the overall value of a building project.
Impact of Advanced Technologies on Building Costs
Incorporating advanced technologies, such as smart home systems, building automation platforms, and advanced security systems, significantly affects the initial building costs. These technologies typically involve the purchase and installation of specialized hardware, software, and networking infrastructure. The complexity of the systems and the level of integration directly influence the overall expenditure.
- Initial Investment: The upfront cost includes the price of smart devices (thermostats, lighting controls, security cameras, etc.), central control units, wiring, and installation labor. For example, a high-end smart home system in a large residential property can easily add tens of thousands of dollars to the construction budget.
- Design and Planning: Integrating these technologies requires careful planning and coordination with architects, engineers, and technology specialists. This necessitates additional design fees, especially for complex projects.
- Customization and Scalability: The level of customization and scalability of the technology also impacts costs. Bespoke systems or those requiring extensive integration with existing building systems will generally be more expensive.
- System Complexity: The more complex the system, the higher the cost. Building automation systems that control lighting, HVAC, security, and other building functions are more expensive than simpler smart home systems that control only a few devices.
Expenses Associated with Installing and Maintaining Technological Systems
Beyond the initial investment, significant ongoing expenses are associated with the installation and maintenance of technological systems. These costs include both tangible and intangible aspects.
- Installation Labor: Skilled technicians are required for the proper installation and configuration of technological systems. Labor costs can be substantial, particularly for complex installations.
- Hardware and Software Costs: Regular updates to software and potential hardware replacements contribute to the ongoing expenses. The lifespan of technological components can vary, requiring eventual replacement.
- Maintenance and Support: Maintenance contracts, technical support, and troubleshooting services are essential to ensure the smooth operation of these systems.
- Energy Consumption: Some technologies, particularly those that run constantly, can increase energy consumption. While many smart technologies are designed to improve energy efficiency, they still require power to operate.
- Training: Training for building occupants or facility management staff to use and maintain the systems can also add to the overall cost.
Long-Term Benefits and Financial Implications of Integrating Smart Technologies
While the initial and ongoing costs of integrating smart technologies can be substantial, the long-term benefits and financial implications often justify the investment. These benefits can lead to significant cost savings and increased property value.
- Energy Efficiency: Smart building systems can optimize energy consumption by automatically adjusting lighting, heating, and cooling based on occupancy and environmental conditions. This can lead to substantial savings on utility bills. For instance, a study by the U.S. Department of Energy found that smart building technologies can reduce energy consumption by up to 30% in commercial buildings.
- Reduced Operational Costs: Building automation systems can streamline operations, reduce maintenance needs, and minimize the need for manual intervention, lowering operational costs.
- Increased Property Value: Smart homes and buildings are often more desirable to potential buyers or tenants, increasing the property’s market value.
- Improved Occupant Comfort and Productivity: Smart technologies can enhance the comfort, convenience, and safety of occupants, leading to increased productivity and satisfaction.
- Data-Driven Insights: Smart systems generate data that can be used to monitor building performance, identify areas for improvement, and make informed decisions about maintenance and upgrades.
Change Orders and Design Flexibility
Change orders, those inevitable modifications to a construction project’s original plans, can significantly impact a project’s budget and timeline. The architectural design plays a crucial role in managing these changes, influencing both their frequency and their associated costs. Thoughtful design anticipates potential issues and provides flexibility, while less considered designs can inadvertently increase the likelihood of costly revisions.
Architectural Design’s Role in Managing Change Orders
Architectural design acts as the blueprint for a construction project, and the quality of this blueprint directly impacts the ease with which changes can be implemented. A well-defined and detailed design, created with thorough coordination among various disciplines, minimizes ambiguities that can lead to change orders. Furthermore, the architect’s ability to communicate the design clearly and concisely to all stakeholders, including contractors and clients, is critical in preventing misunderstandings and subsequent modifications.
Proactive design, incorporating elements of flexibility and adaptability, can also mitigate the impact of unforeseen circumstances or evolving client needs.
Design Choices Increasing the Likelihood of Change Orders
Certain design choices can make a project more susceptible to change orders. These choices often stem from a lack of foresight or a failure to consider the practicalities of construction.
- Complex Geometries: Designs featuring intricate shapes, curves, and non-standard angles often require specialized fabrication and installation techniques, increasing the potential for errors and necessitating modifications. The more complex the design, the higher the risk of unforeseen challenges during construction.
- Uncoordinated Systems: Poor coordination between different building systems (e.g., mechanical, electrical, plumbing) can lead to clashes and conflicts during construction, requiring costly revisions. For example, a ductwork layout that interferes with structural elements necessitates redesign and rework.
- Lack of Detail: Incomplete or ambiguous drawings leave room for interpretation and potential errors by contractors. This lack of clarity can lead to discrepancies between the intended design and the actual construction, resulting in change orders to rectify the issues.
- Unrealistic Material Specifications: Specifying materials that are difficult to obtain, expensive, or not readily available in the construction market can force the project team to find alternatives, which may necessitate design changes and approvals.
- Failure to Consider Site Conditions: Ignoring site constraints, such as soil conditions, existing utilities, or environmental regulations, can lead to unforeseen problems during construction. For instance, if the foundation design is not appropriate for the soil type, the foundation may need to be redesigned, resulting in change orders and associated expenses.
Methods for Designing Buildings with Built-in Flexibility
Designing buildings with inherent flexibility can significantly reduce the need for costly modifications during construction and over the building’s lifespan. Several strategies can be employed to achieve this.
- Modular Design: Utilizing modular components allows for easier adaptation and expansion. Modular construction allows for standardization, reducing construction time and minimizing the need for site-specific adjustments.
- Open Floor Plans: Open floor plans provide greater flexibility for future space reconfiguration. These designs typically feature fewer load-bearing walls, allowing for easier changes to room layouts.
- Standardized Systems: Employing standardized building systems, such as HVAC, electrical, and plumbing, simplifies installation and maintenance, and also facilitates future modifications. Standardized systems are easier to understand, install, and repair, which reduces the likelihood of errors and the need for change orders.
- Accessible Building Services: Providing easy access to building services, such as electrical and plumbing systems, facilitates maintenance and modifications. This can include access panels, raised floors, and accessible ceiling spaces.
- Anticipating Future Needs: Considering potential future needs during the initial design phase, such as expansion, technological upgrades, or changes in use, can help to incorporate flexibility into the building’s design. For example, designing for future expansion by providing additional structural capacity or allocating space for future equipment.
Procurement and Construction Methods
The architectural design profoundly influences both the procurement of materials and the selection of construction methods. These choices significantly impact project costs, timelines, and overall feasibility. A well-considered design streamlines the procurement process, reduces waste, and allows for the adoption of cost-effective construction techniques. Conversely, a poorly planned design can lead to delays, increased material costs, and the need for costly on-site modifications.
Design Impact on Procurement and Construction Choices
The architectural design acts as the blueprint for all subsequent activities, including material acquisition and the construction process itself. The complexity of the design, the specified materials, and the required precision dictate the ease and cost-effectiveness of procurement and construction.
- Material Specifications: The design specifies the types, quantities, and quality of materials needed. Precise specifications minimize material waste and allow for competitive bidding from suppliers. Vague specifications can lead to over-ordering, delays, and disputes.
- Construction Methods: The design dictates the construction methods that are feasible. Complex designs may necessitate specialized construction techniques, such as prefabrication or modular construction, which can affect costs and timelines.
- Procurement Strategy: The design influences the procurement strategy. A design that incorporates standard, readily available materials allows for easier and more cost-effective procurement. Conversely, a design requiring custom or specialty materials can lead to longer lead times and higher costs.
- Project Scheduling: Design details influence the project schedule. Complex designs with intricate detailing often require longer construction periods, increasing labor and overhead costs.
Cost Implications of Different Construction Methods
Different construction methods carry distinct cost implications, often impacting the overall project budget. The choice of method should align with the design’s requirements, the project’s location, and the available resources.
The cost of construction is significantly influenced by the method employed. Consider the following:
- Prefabrication: Prefabrication involves manufacturing building components off-site and assembling them on-site. This method often leads to cost savings due to reduced labor costs, faster construction times, and less material waste.
- Cost Advantages: Reduced on-site labor costs (typically 10-20% savings), faster project completion (reducing financing costs), and better quality control due to factory-controlled environments.
- Cost Disadvantages: Transportation costs for prefabricated components, potential limitations in design flexibility, and the need for specialized equipment for installation.
- Example: A study by McKinsey & Company found that modular construction can reduce project costs by up to 20% and construction time by up to 50%.
- On-Site Construction: This traditional method involves building structures directly at the project site. While it offers greater design flexibility, it often involves higher labor costs and longer construction timelines.
- Cost Advantages: Flexibility to adapt the design during construction, suitability for complex or unique designs, and potentially lower transportation costs for materials.
- Cost Disadvantages: Higher labor costs, longer construction times, susceptibility to weather delays, and greater potential for material waste.
- Example: Traditional stick-built homes often experience cost overruns due to unforeseen site conditions, weather delays, and changes during construction.
- Hybrid Approaches: Many projects employ a hybrid approach, combining elements of both prefabrication and on-site construction to leverage the benefits of each method.
- Cost Advantages: Offers a balance between design flexibility and cost efficiency.
- Cost Disadvantages: Requires careful coordination between off-site and on-site activities to avoid delays and cost overruns.
- Example: A project might use prefabricated wall panels and a traditionally constructed foundation to optimize both speed and design adaptability.
Designing for Cost Minimization through Procurement and Construction
To minimize expenses, the architectural design should be strategically aligned with the procurement process and chosen construction methods. This involves careful consideration of material selection, design simplification, and construction feasibility.
- Standardization and Modular Design: Designs that incorporate standard components and modular elements simplify procurement and construction.
- Material Optimization: Selecting readily available, cost-effective materials and minimizing material waste.
- Design for Constructability: Designing structures that are easy to build, reducing labor costs and construction time.
- Early Procurement Planning: Planning for material procurement early in the design phase, allowing for competitive bidding and timely delivery.
- Value Engineering: Employing value engineering techniques to identify cost-saving opportunities without compromising the design’s functionality or aesthetics.
Closing Summary
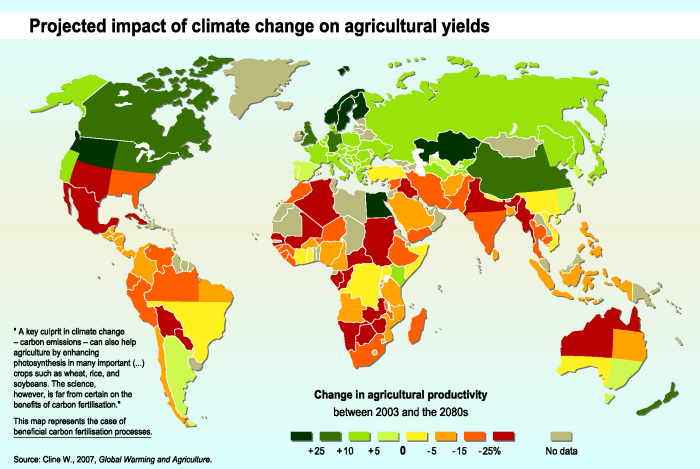
In conclusion, the impact of architectural choices on cost is multifaceted and profound. From the initial design phase to the integration of advanced technologies, every decision carries financial implications. By carefully considering material selection, building complexity, energy efficiency, and other key factors, stakeholders can optimize project budgets and achieve sustainable, cost-effective designs. This understanding empowers informed decision-making, leading to successful construction projects that meet both aesthetic and financial goals.
Commonly Asked Questions
How early in the design process do architectural choices start affecting costs?
Cost impacts begin in the initial planning and design phase, as early decisions on building form, materials, and systems can significantly influence overall project expenses.
Can sustainable design actually save money?
Yes, sustainable design can reduce long-term operational costs through energy efficiency, lower water consumption, and reduced maintenance expenses, often offsetting higher upfront costs.
What is the impact of change orders on project costs?
Change orders can significantly increase project costs due to rework, material changes, and delays. Architectural design plays a crucial role in minimizing the likelihood of change orders by ensuring clarity and flexibility.
How does the choice of construction method affect cost?
Different construction methods, such as prefabrication versus on-site construction, have varying cost implications. Prefabrication can often reduce labor costs and shorten timelines, while on-site construction offers more design flexibility.